Full-Length Tube Coating
Versite ® Tube Repair and Protection System
Discussion
The tubes used in steam condensers and other balance of plant heat exchangers are selected such that they will provide many years (decades) of reliable service. In the case of heat exchangers, reliable service generally consists of being leak free with acceptable heat transfer properties. Tube materials are specified with regard to expected water chemistry, cleanliness, and cost. However, due to unforeseen circumstances or to operational anomalies, tubes may begin to form pits, which if not mitigated or otherwise controlled, can result in tube leaks. In most cases, the tube must then be identified and plugged. Significant costs are incurred locating and plugging a tube, all because of a single pit. Identifying the mechanisms for pit formation and understanding how to control these processes is an important aspect of the maintenance of steam condensers and other heat exchangers. With copper alloy tubes, the tube also generally thins over time with the wall loss usually being greater towards the outlet end, due to increased temperatures. In some waterways this loss of copper is also a concern from an environmental perspective (copper ion release) and is closely monitored and controlled.
Conventional Responses and Remediations
While the response to tube pitting depends on the situational specifics, one or more of the following actions are generally followed:
- Improved cleanliness – The underlying cause of many pitting phenomena is a lack of cleanliness. The removal of tube deposits and the installation of better tube cleaning methods may be sufficient to stop tubes from further deterioration.
- Chemical treatment – While general chemical treatments are usually a means to better cleanliness (scale reduction/corrosion control), other treatments utilizing biocides or oxidizing agents can be used to control biological activity which is initiating the pitting.
- Eddy current testing and preventative plugging. Due to the depth and/or morphology of the pits, the conventional tools may not be effective in stopping existing pits from continuing to grow. In this case it may be necessary to identify those tubes with deep pits (usually via eddy current testing) and to preventatively plug those tubes. This is only effective as long as the underlying cause for the pitting has been identified and corrected.
- Retube – In severe cases, where the pitting cannot be effectively be controlled, or an unacceptable amount of tubes have been lost, the tubes must be replaced. In this case care must be taken to choose a more appropriate tube material or take steps to insure that the conditions which caused the original pitting do not reoccur.
New Tube Repair and Protection Method
In addressing the specific issues associated with pitting of power plant condenser and heat exchanger tubing, a new approach to tube coating has been devised. The root of this approach is a change of emphasis from that of conventional coating. This approach has gained patent protection. (US 7,270,847 B2; 7,717,056 B2).
Using our patented Squeegee Pig design, the object of this method is to fill pits and other defects in the tube wall while leaving a very thin protective layer on the rest of the tube interior. In essence, this method serves to “spackle” the tube wall. For holes, the coating will exude through the tube wall to the tube exterior. This forms an epoxy “rivet” which permanently seals the hole. For tubes with highly irregular erosion and corrosion patterns, the coating serves as a fairing compound and will smooth out the surfaces.
Coating the full length of tube interiors is a useful tool to manage the performance and life span of main steam condensers and balance of plant heat exchanger tube stock. Coatings can provide a variety of benefits including arresting tube failure rates and the return of plugged tubes to service.
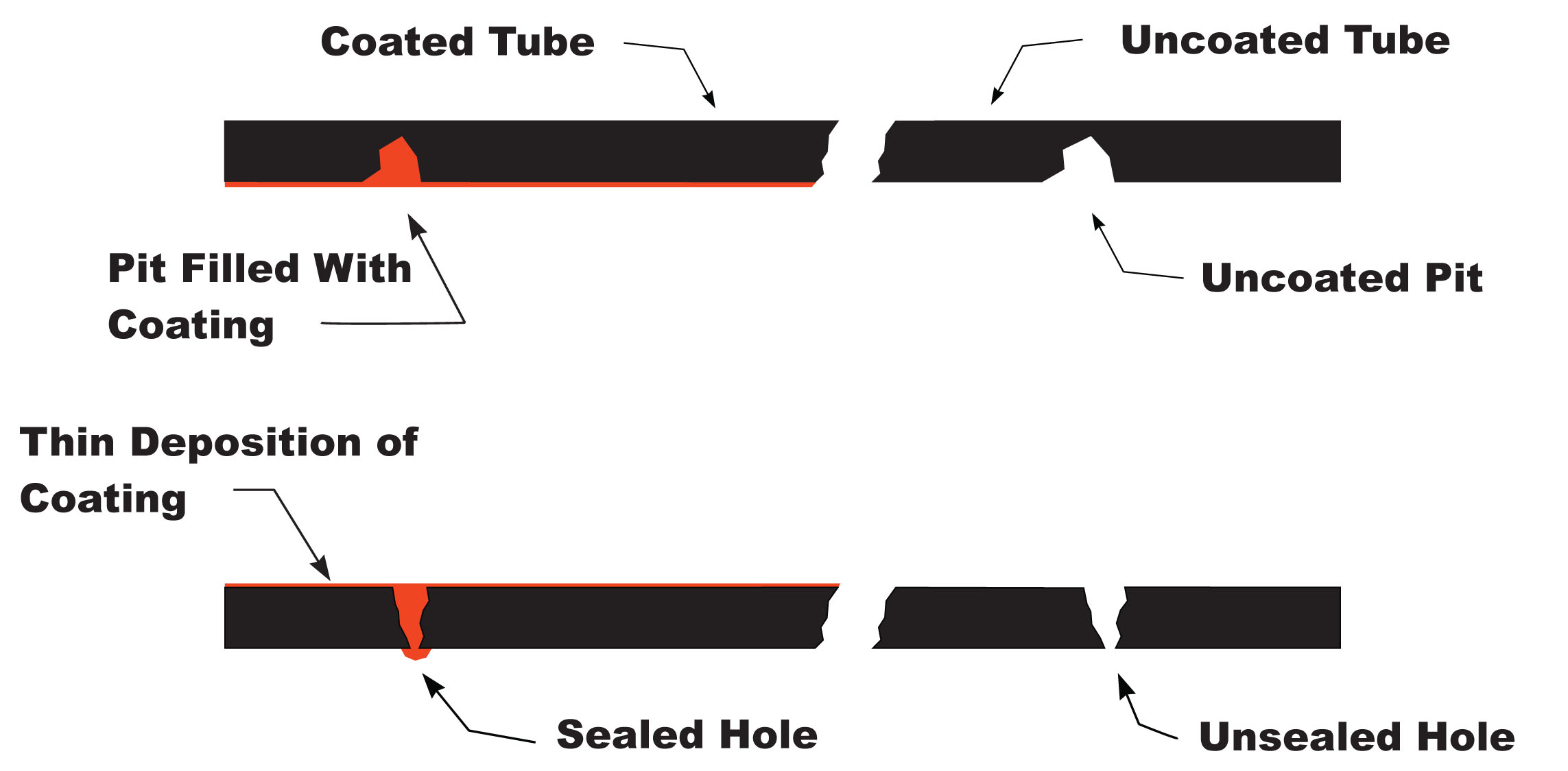
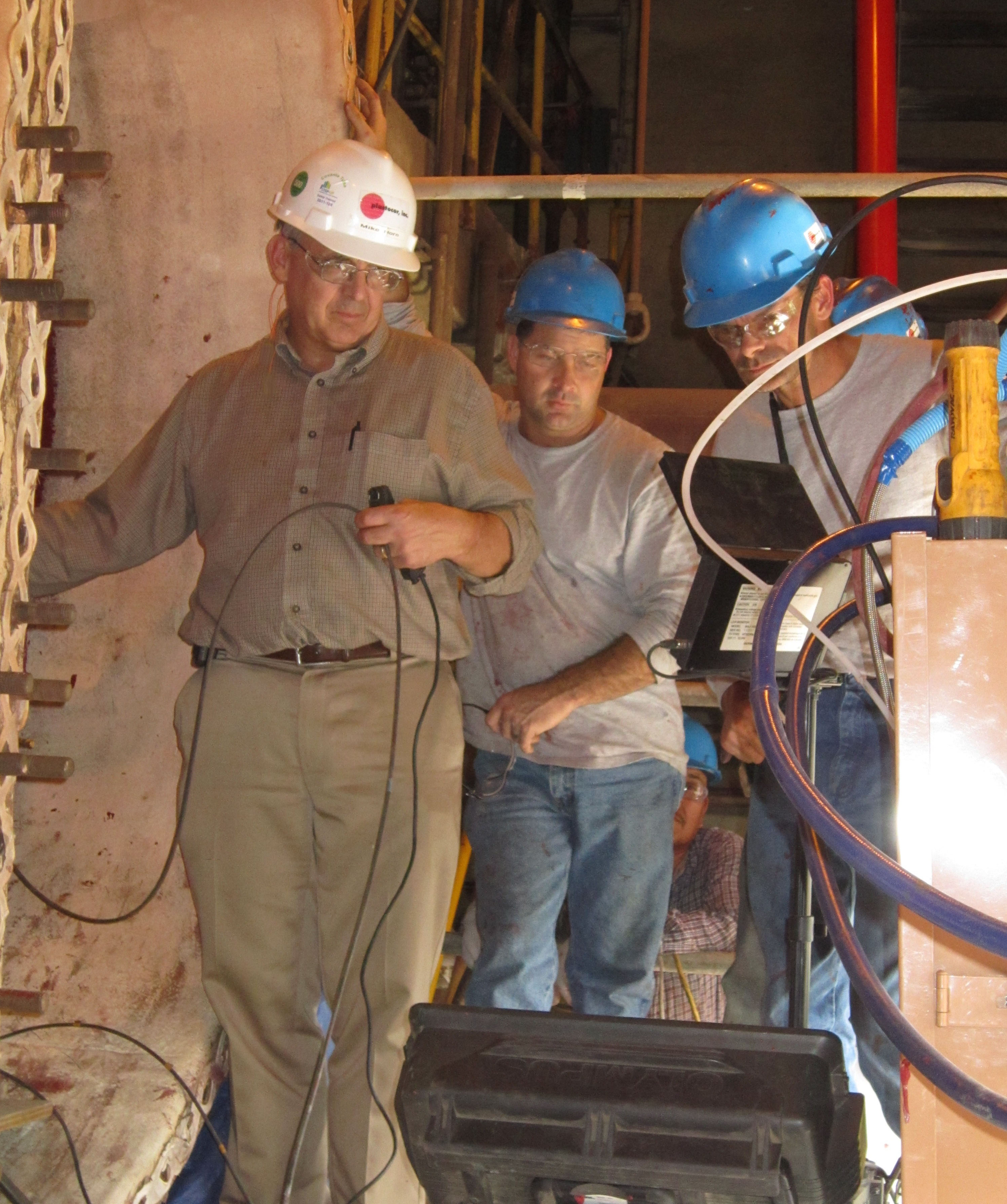
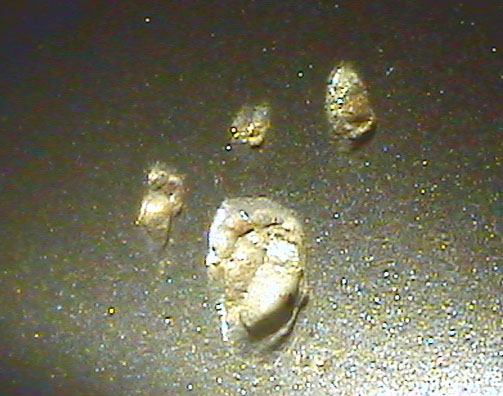
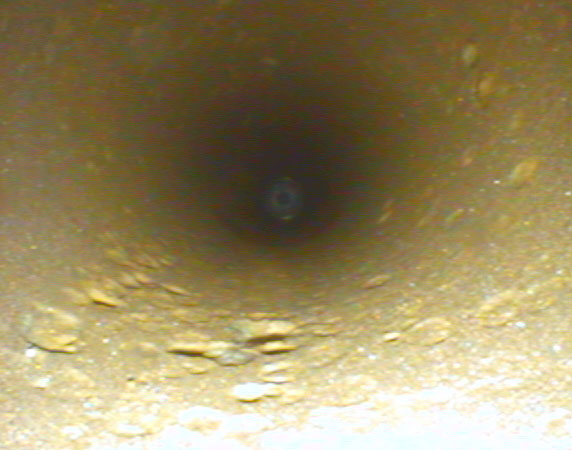
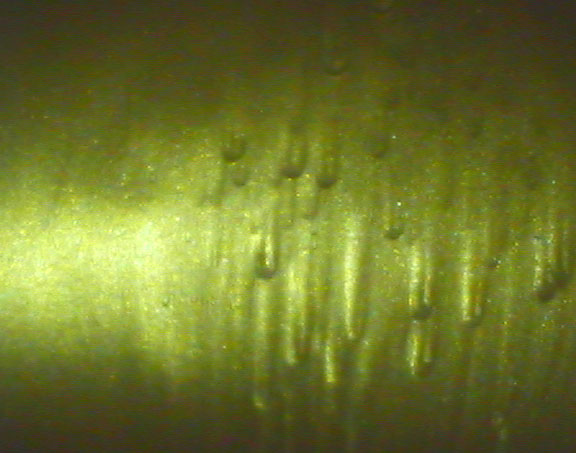
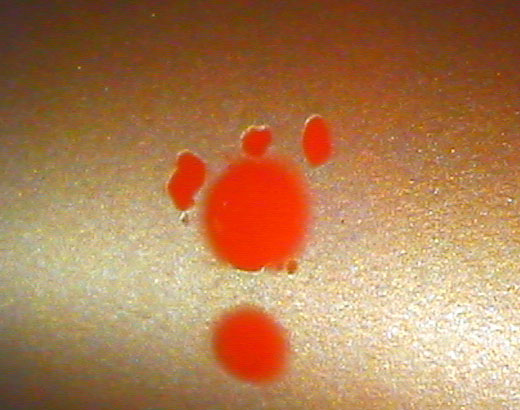
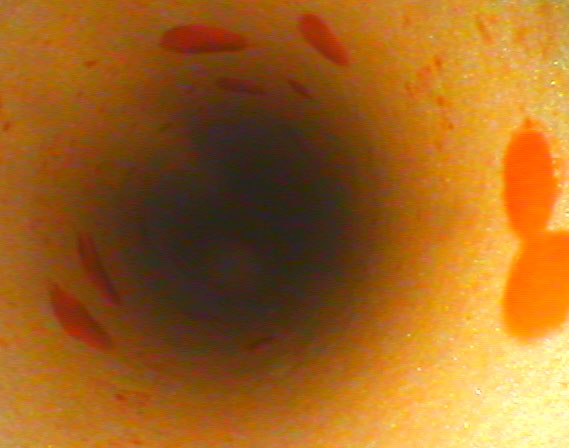
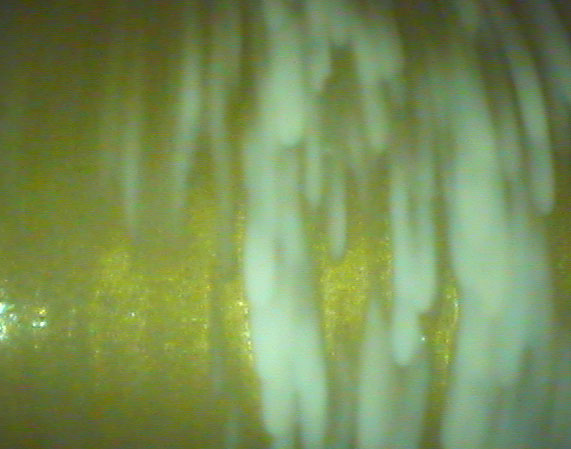
Featured Project
In the Spring of 2012 a 1950’s vintage natural gas unit located on a lake in Texas encountered multiple condenser tube failures of its Admiralty Brass tubes. Due to time and cost restraints, the option of retubing was not chosen to prepare the unit for the summer run. Instead, the full-length of approximately 5,500 tubes were epoxy coated. This included 1,150 tubes which had been plugged as leakers, but were unplugged and coated using a special leak sealing method of applying the epoxy lining. The coating process was completed in 10 days and all but 55 tubes were sealed by the coating process. These tubes were plugged and the unit was put into service. The unit has been running successfully since the project was completed with no heat rate penalty. The images below are from this project.
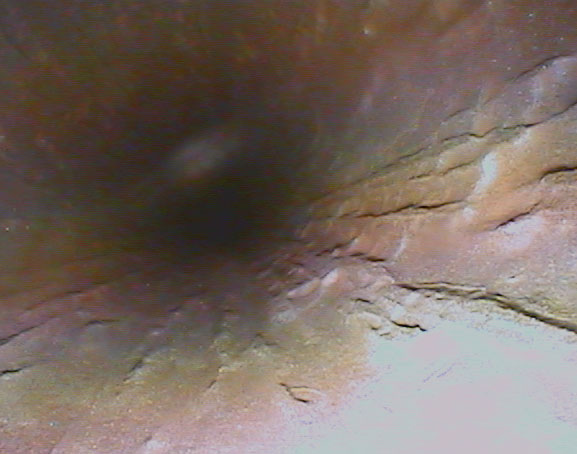
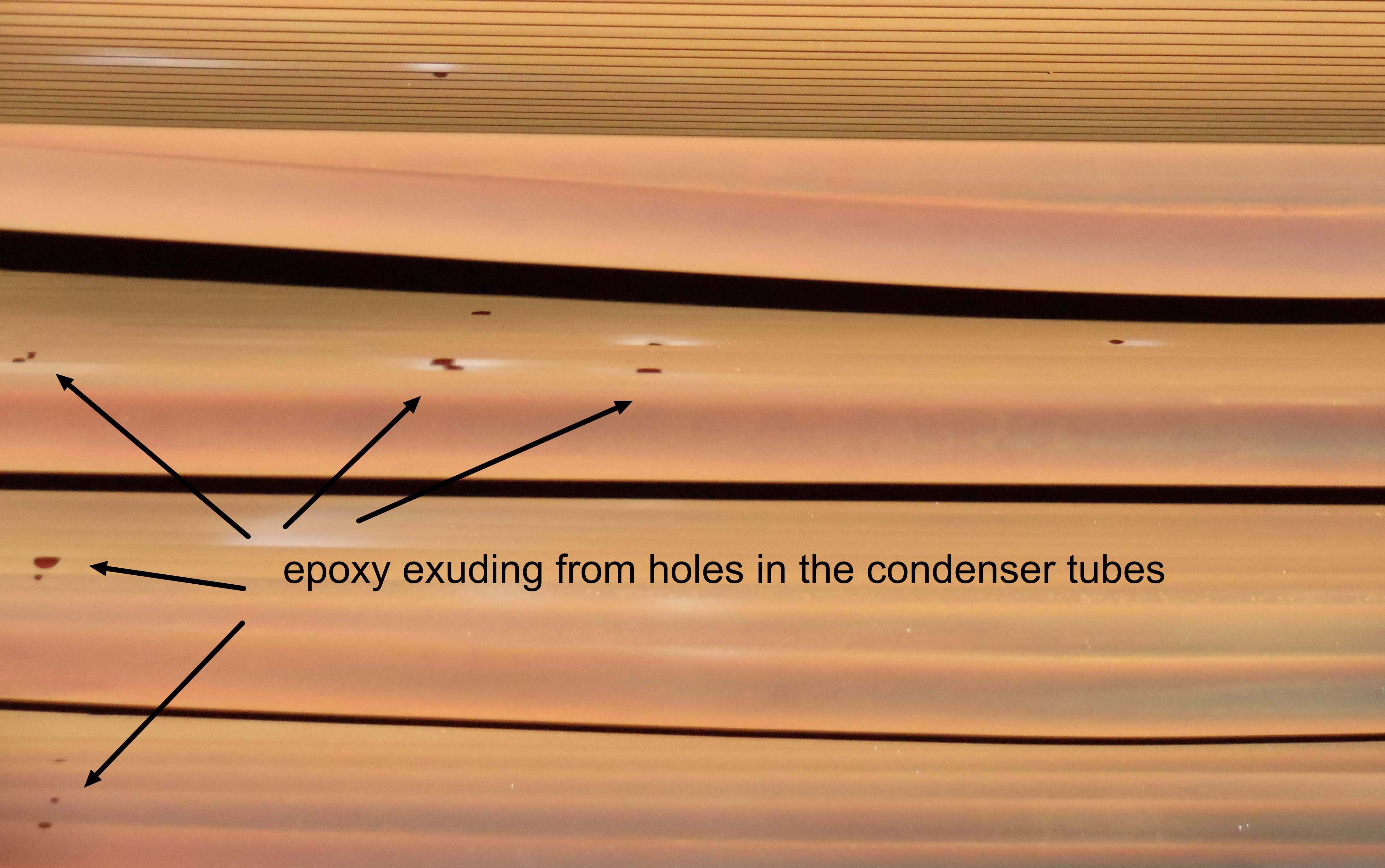
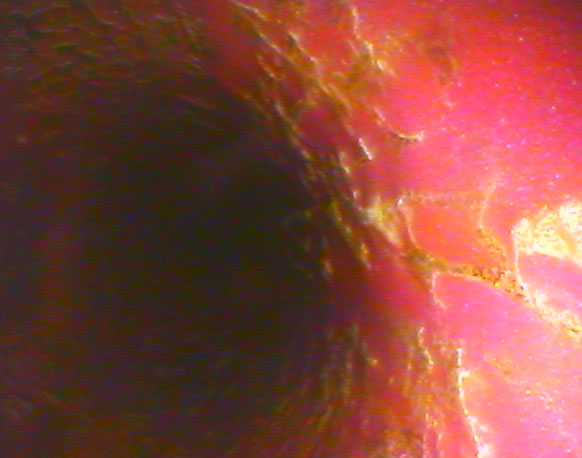